Slip Clutch
In The Baja SAE design competition, reliability is everything. As a part of my capstone design project, I developed this slip clutch to protect our bevel gears and driveshaft from extreme loads while still taking advantage of the extra performance of a driven front axle. My clutch was designed to take advantage of the full engine torque (300 ft*lbs at this reduction stage, 515 ft*lbs at the wheel), but slips if the torque goes beyond that. This gives our car an edge because it improves drivetrain reliability while still taking advantage of performance and weight reduction.
Background:
Northeastern Baja’s first attempt at a slip clutch was done for the 2022 car. This clutch was rated for 250 ft*lbs at the wheel. It was not adjustable and relied on pre-loading belleville washers to hold torque. At 4WD check for the Baja SAE competition, this clutch failed multiple times to deliver torque to the front wheels. It eventually passed, but that experience placed adjustability and reliability atop the list of requirements for the new design I was to begin working on.
2022 Slip Clutch
My slip clutch is based on commercially available slip clutches, but is much larger to handle a much greater torque. There is an input shaft which takes torque from the transfer case output and translates it to the hex machined onto the shaft.
Off-the-shelf slip clutch from Dynatect
Design and Calculations:
Using the system integration design requirements, I set to work on design calculations and CAD iterating through CAD revisions to design a solution that would fit the packaging requirements, be manufacturable, and tunable. First, I created a spreadsheet to make calculations based on the equations used by the brakes subteam to size hydraulics based on the interaction between the brake pads and brake rotors. These calculations helped me balance the trade-offs in determining the number of springs, number of friction pads, spring rate, and max adjustability.
With component, torque, and required forces decided, I began the CAD design in solidworks. I used Aluminum wherever possible, for lightness and ease of machining, 4130 for the wear surfaces, and 4340 for the central shaft where high strength was required. The design was done in coordination with the designers of the upstream and downstream drivetrain components to ensure that the slip clutch would adequately protect those parts, and that the packaging would interact in a serviceable manner.
Manufacturing:
In compliance with the rules of the Baja SAE competition, I manufactured the entire slip clutch myself. I designed all parts from the beginning to be optimized for the advantages and drawbacks of the CNC lathes and mills the team had available,



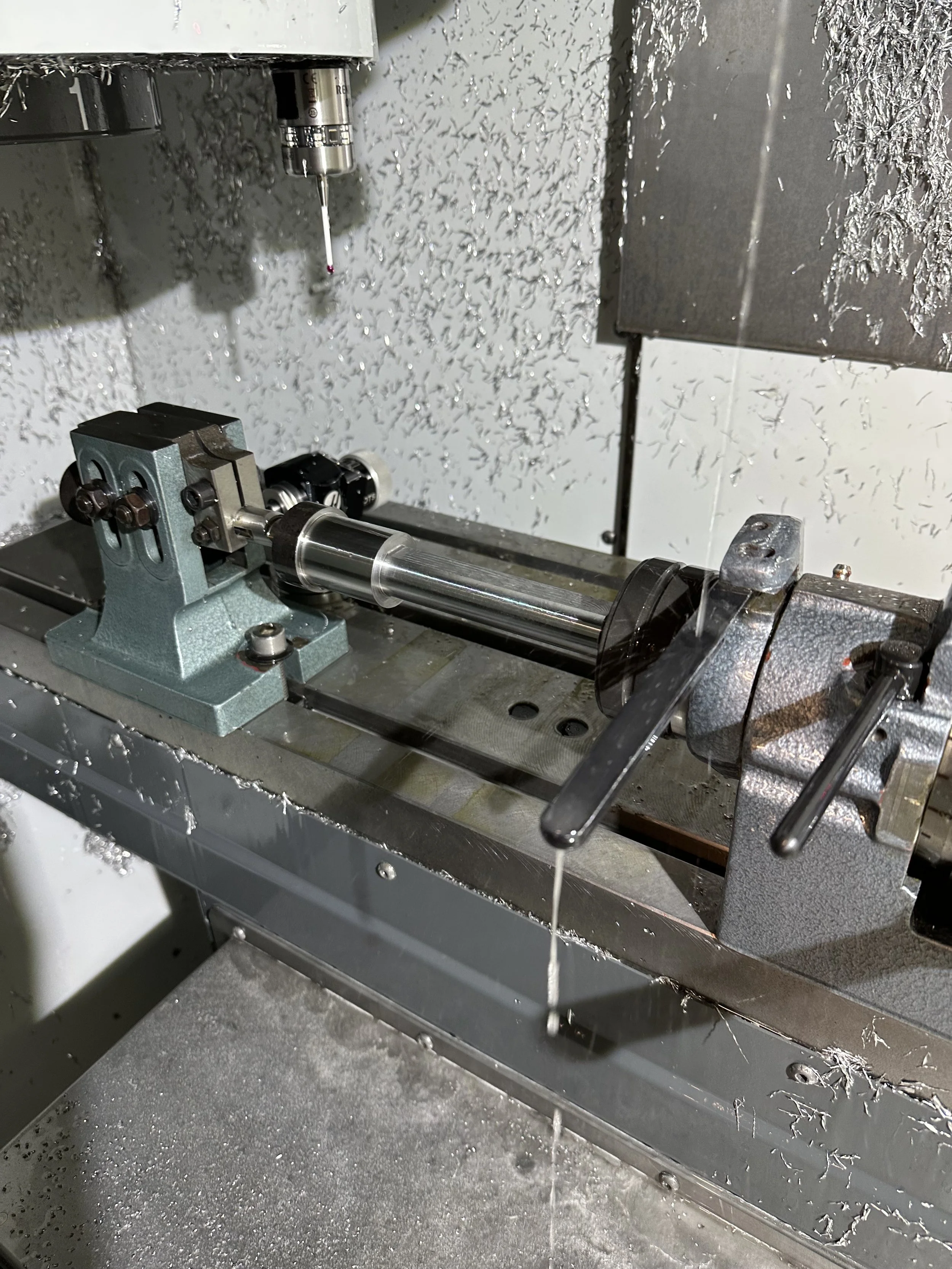
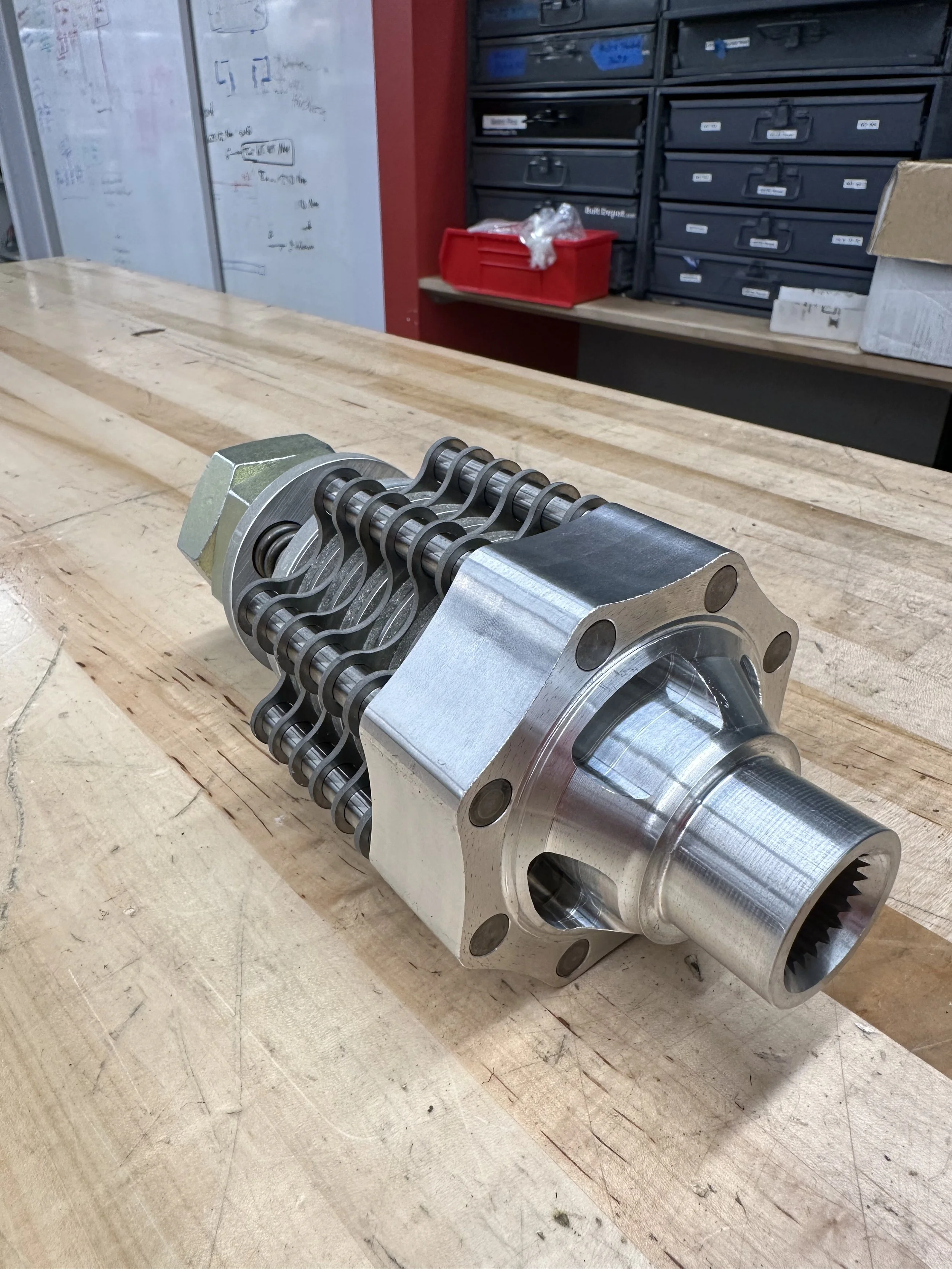
Testing
To test the slip clutch we did component and system level testing to confirm the effectiveness of the slip clutch. We used a torque wrench to determine the static torque able to be held by the clutch as a function of the spring compression. This allowed us to get a baseline for slip clutch setup to validate my analysis and correctly protect our drivetrain components. It was a crude setup, but I think it is a great example of avoiding becoming paralyzed looking for perfection, and instead rolling with the resources we had available.
On the more developed end of the testing suite, we also did system level testing using two hall effect tachometers that I designed and programmed to determine if the slip clutch was engaged or slipping during normal driving. This system uses two custom Arduino boards with hall effect tachometers to measure the speed on each end slip clutch. One side is directly on the driveshaft, and one is on the output shaft to the rear wheels, which is rigidly linked to the slip clutch input shaft through the static gear ratio of the gear reducer box and the bevel gear transfer case.